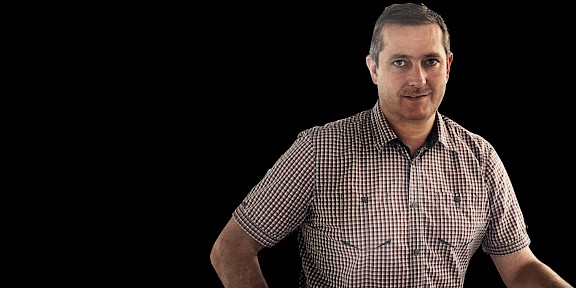
Employee Story Klaus Kienle, Quality Management Officer (QMB) Quality is not a coincidence, it is always the result of hard work and thought
My name is Klaus Kienle, I am married, have 3 children and live in Oberstetten. I enjoyed my training as an Industrial Mechanic at the Vollmer works in Biberach an der Riss. Thereafter I was employed in the assembly of grinding machines for carbide circular saw blades. I led out the work from assembly to testing and acceptance of the entire machine to training customers on the machine and commissioning at the customer's site. In 2002 I began further training as a state-certified technician - specialising in Machine Technology - which I successfully completed in summer 2004. I have been working here at Wölfle in Quality Assurance since September 2004. Since then I have been able to acquire a lot of knowledge in the area of quality assurance. From October to December 2008 I received additional training from quality management specialists to quality management officers and quality management auditors. Then I took on the task of QMB and the management of quality management. In addition, I was given the job of managing test equipment. To this day, I am leading and performing these tasks with a lot of joy and commitment. In doing this job, I have to deal with a large number of people - both internally and externally - which is of course a great challenge.
-
Seit 16 Jahren
at Wölfle
-
2002
Further training to become a technician
-
Problemlöser
QS
-
Zertifikat
ISO 9001:2015
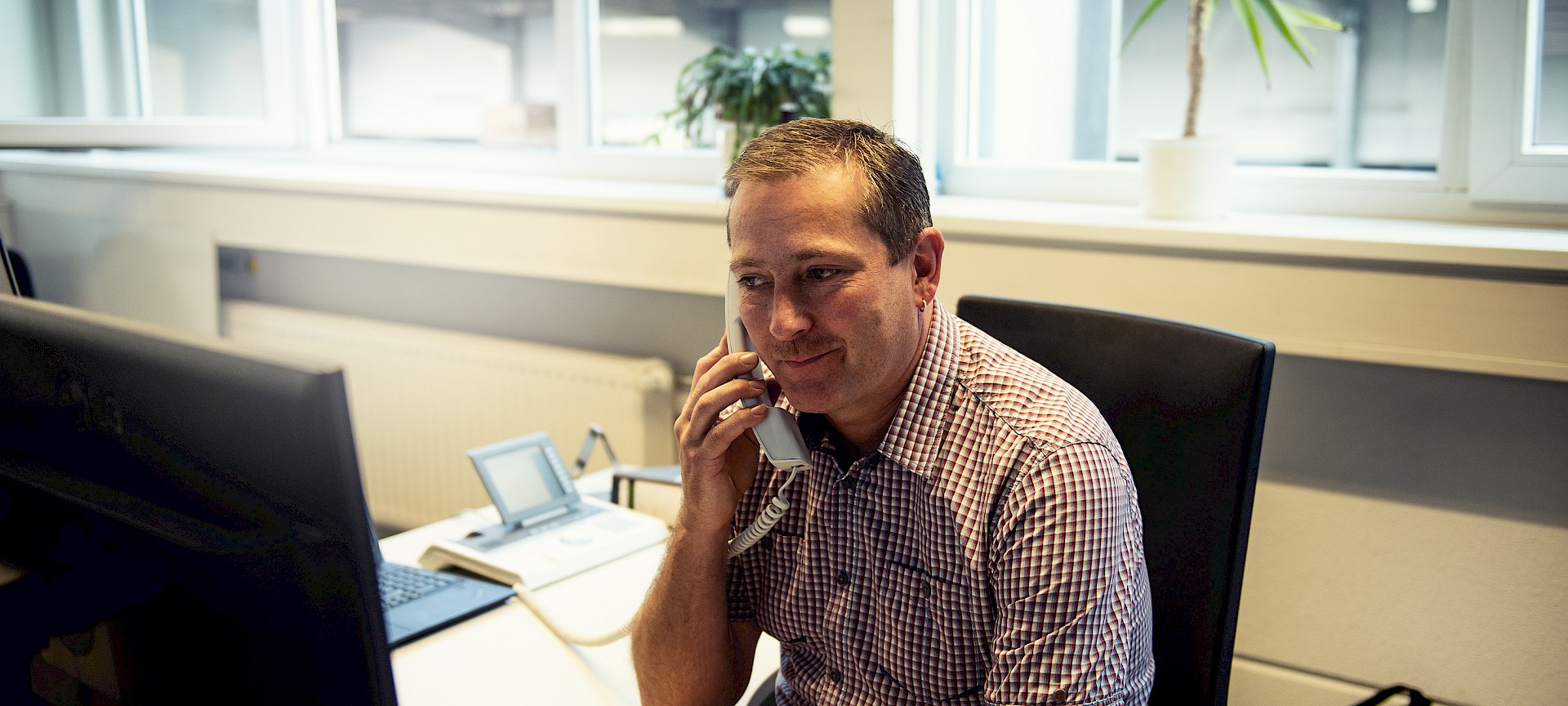
"Oh now comes the QA again"
With this sentence we are always greeted by our colleagues. The fact is that we - QA - take the position in the company that looks at things with the “customer's eye”. When it comes to complaints and problems, we are the interface between the company and the customer and supplier. Unfortunately, it is also one of our tasks to convey negative reports to our colleagues. However, our motto is solve the problem, not the question of fault.
We are a young, motivated and committed team that always has an open ear for everyone - be it internal or external. Our area of responsibility at Wölfle is very diverse. It already begins in the development phase of a product. We are happy to be included with our experience so that past problem points are taken into account for new and current products. We are also called on in the ongoing series with all problems - be it with purchased parts or with in-house production parts.
Unfortunately, after the delivery of our products, there are sometimes complaints. Here we are the first point of contact. We get in contact with the customer and process the complaints. Every processing step is recorded and maintained in the QAM module of our ERP system. This includes troubleshooting, error analysis, the initiation of measures and thus eliminating the cause of the error. In doing so, we can fall back on the respective specialist departments and specialists throughout the company. Because only satisfied customers become good customers and the aim of every employee should be that it is not the product that comes back, but the customer that comes back to us.
We work with the same process towards our suppliers. We record complaints from our colleagues and forward them to the suppliers. Here we also request an analysis up to and including the corrective measures. With incoming goods inspections, we ensure that only parts are stored that meet our specifications and quality requirements.
The test equipment monitoring, i.e. the calibration and monitoring of the quality of the test and measuring equipment, is also carried out by us. We ensure that tests can be carried out at any time with calibrated testing and measuring equipment that is in proper condition.
Another important task is the preparation, implementation and support of audits. These can be audits at our suppliers on site, but also by customers in our company or by certification companies such as TÜV Süd. In July of this year, the 8th Repeat Audit according to ISO 9001 with KBA was due. Together - and we're talking about all of our colleagues - we successfully completed the audit, so that we received the ISO 9001:2015 certificate and the KBA certificate supplement once again.
We hope we were able to bring our department a little closer to you with this short excerpt.