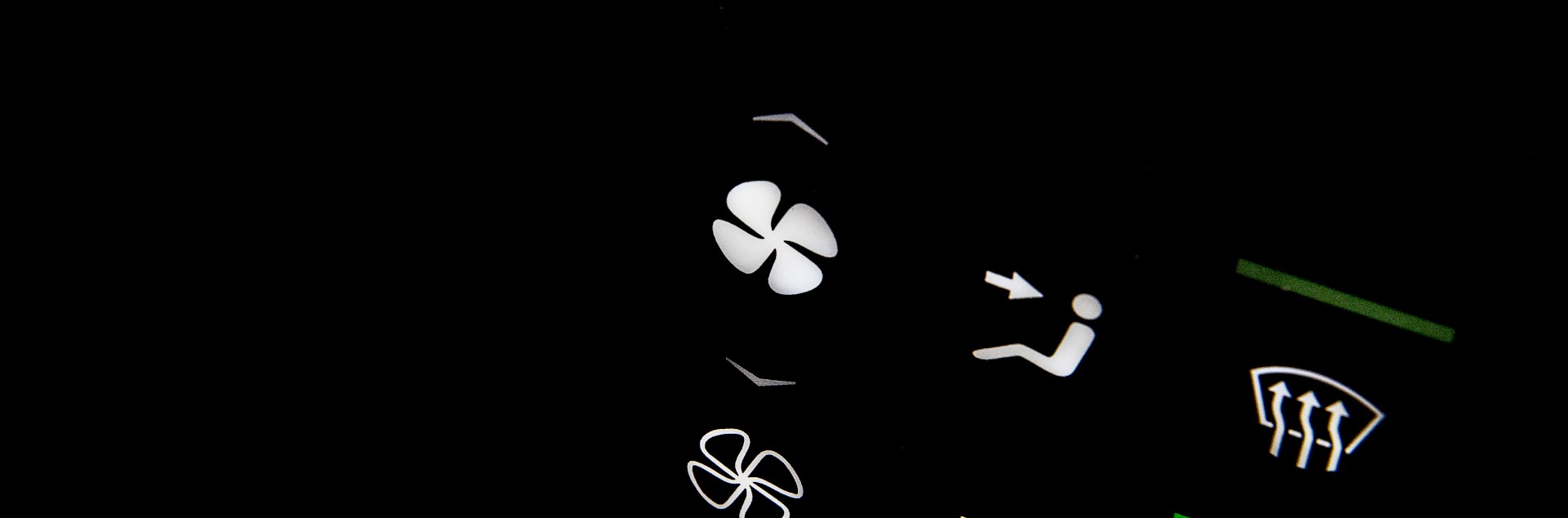
Thermal management Tailor-made thermal management solutions – for maximum efficiency and service life of modern vehicles
Alternative drives pose new challenges for many vehicle manufacturers. Particular attention is paid to the range, service life, costs and ultimately also efficiency.
Wölfle has been dealing with the topic of E-mobility for years and is has been working with many OEMs as research and system partners on the vehicles of tomorrow. As early as 2008, the company developed one of the first cooling systems for commercial vehicle batteries in order to efficiently increase the service life of the batteries through active cooling.
By expanding this technology, Wölfle has been able to successfully implement a multi-circuit liquid system with a reversing heat pump in addition to various component cooling systems with mathematical climate models.
Thanks to the combined expertise in the HV/AC area and model-based control, we are able to implement even the most demanding solutions for your thermal management.
-
Central Thermal Management
Wölfle heat pump
-
<1K
Temperature accuracy
-
Mathematical energy model
Thermal management
-
Maximum Range
Waste heat utilisation & preconditioning
It is not uncommon for vehicles to have to be converted from the point of view of thermal management because the energy flows during operation are different from what was theoretically expected. With the thermal management model from Wölfle, each component can now be connected to the system according to its specifications, performance and temperature level. It can also be flexibly adapted to any vehicle.
Background thermal management
Modern or future vehicles are increasingly becoming purely electric vehicles. The focus is not only on cars, but also on more and more mobile work machines that have to be operated purely electrically. Because here, too, emissions regulations are mainly in the room as a motivator. In some areas, such as forklifts, this has been standard for years. When vehicles become E-vehicles, the fuel is replaced by a battery. In some cases also by a fuel cell, by solar cells or by a cable. All of these vehicles therefore have a problem: The waste heat that was previously available as a waste product from the combustion process must be generated electrically. The energy required for this can halve the operating time or the range under unfavourable circumstances. The efficiency of energy consumers suddenly plays a very important role. This applies in particular to heating and air conditioning systems, but other components such as the battery or fuel cell, power electronics or charge controllers have special thermal management requirements that need to be solved.
Functionality of components from the point of view of thermal management
Battery: In some cases, the battery is a very maintenance-intensive component that can only be operated within a certain temperature window. The service life is reduced from an operating temperature of + 40° C, while below –10° C the efficiency decreases and the performance decreases. In addition, the temperature difference between the individual cells must not exceed a certain value, as this also reduces the service life. To make matters worse, short-term peak stress in connection with high currents such as recuperation and boosting lead to a not inconsiderable warming of the cells.
HVAC system: The heating/air conditioning system is a neglected component in many projects. Achieving good comfort in the interior is only possible with certain operating points, but these are often at different temperature levels than the components in thermal management. A mere performance assessment is not possible here, as people are very sensitive to temperatures and air volumes. For example, the highest possible blow-out temperature (& gt; 60° C) should be selected in heating mode. However, the maximum operating temperature of batteries is usually around 40° C. If you would now want to heat at 40°C, this can only be implemented with significantly more air, which can have a strong effect on the volume level.
Electric drivetrain: The components of the electric motor, power and charging electronics usually provide thermal energy that has to be dissipated both when driving and when charging. These can best be compared with the combustion engine as an energy supplier. The overheating protection should also be observed here, especially when charging e.g. overnight.
Fuel cells: The process in the fuel cell also releases heat that has to be dissipated. The temperature levels correspond to approximately 80° C and are comparable to an internal combustion engine.
Function of thermal management
Wölfle understands the function of thermal management as the perfect distribution and adjustment of the heat flows. The central starting point is a complex mathematical model that controls the currents, taking into account the heat requirements including their temperature levels, homogeneity and temperature accuracy. Here, different flow channels, such as e.g. water circuits, refrigerant circuits, air currents or convection can be taken into account and selected. It is also possible to direct the flows through amplifiers such as heat pumps or other components such as outside air units, auxiliary heaters or storage tanks. The aim is to collect and use as much energy as possible in order to make it ideally available to the components. Thermal management is there to fulfil the protective function for components and to provide consumers such as the heating/air conditioning system with the necessary energy. In general, the following added value can be achieved
- Extension of range or deployment time.
- Better and more efficient heating/air conditioning and comfort functions
- Increase in the service life of batteries, electronics, etc.
- Improvement of the emission values
- Integration of special functions such as preconditioning, charge cooling, etc.
Experience from numerous projects shows that the focus must always be on costs, installation space and technical limits.
Advantages of the Wölfle approach
Wölfle creates a holistic Thermal Management Model which can be adapted to any vehicle in a highly flexible manner. The patented system is able to connect every component to the system according to its specifications, performance and temperature level. Depending on the requirements, the individual components are connected by means of water cooling circuits. The central point is the control electronics, which distribute the energies using various energy and control models. The distribution takes place by means of various actuators, pumps and chillers. In addition, it is possible to integrate further components for energy production or dissipation. These include, for example, heat pumps, electronic PTC heaters, air-water coolers, etc. The end result is a highly flexible fluid system that can be installed in the initial prototype vehicles. During the subsequent testing of the vehicle, measurement and model data can then be collected using in-house tools, which are then evaluated for specific applications. The aim of the evaluation is a cost-benefit comparison that shows relatively quickly which networking makes sense in the future vehicle and which not.
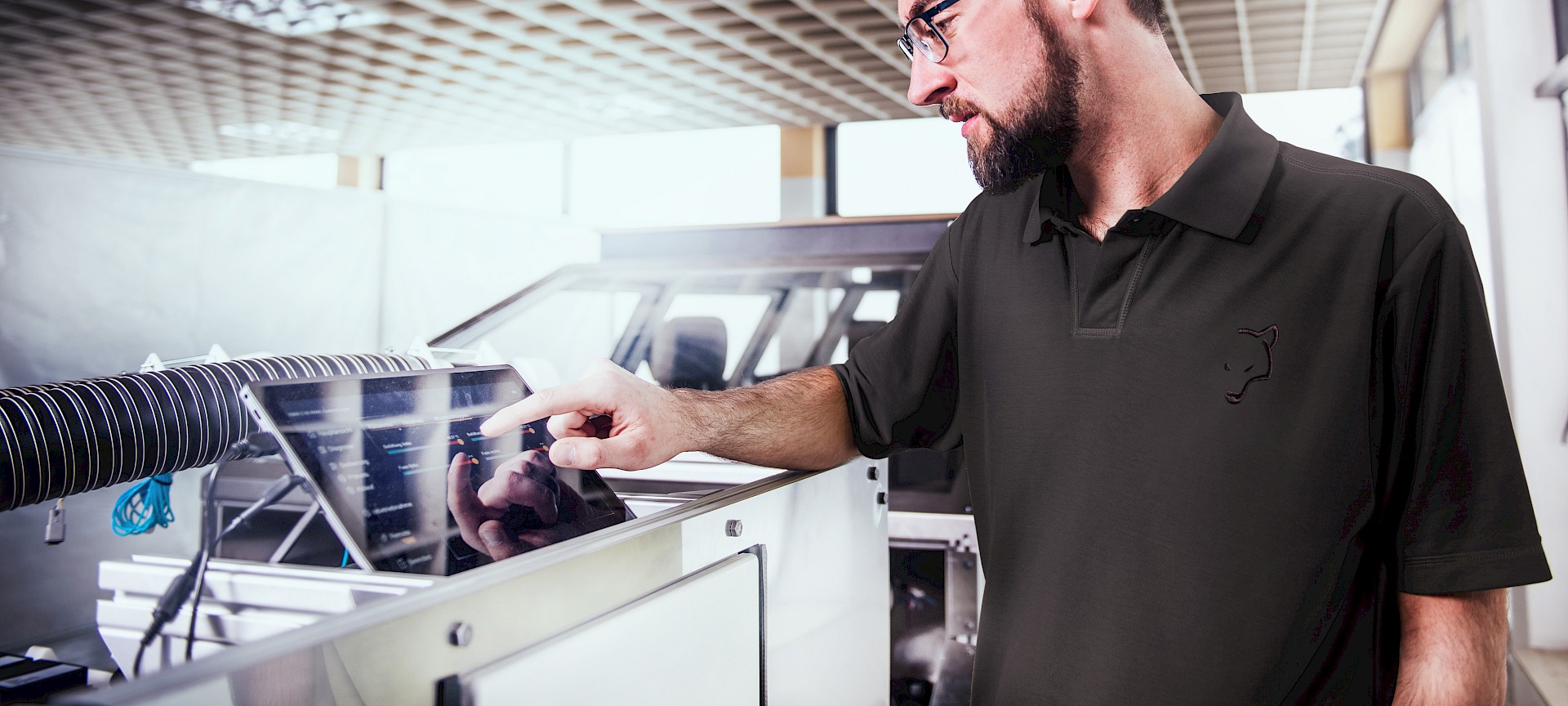
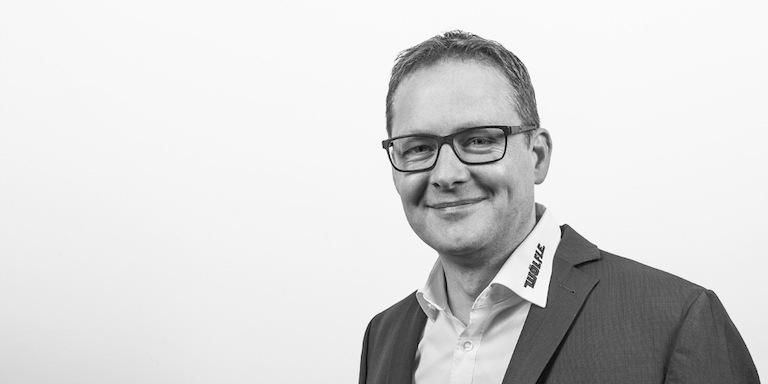
Markus Reich
Key-Account-Manager
Cabs Distribution
T +49 (0) 7352 / 929 130